News and Insights
E-commerce, Logistics, and Small Business Management
Retail Season 2020: Three Operational Risk Factors as eCommerce’s Peak Season Approaches
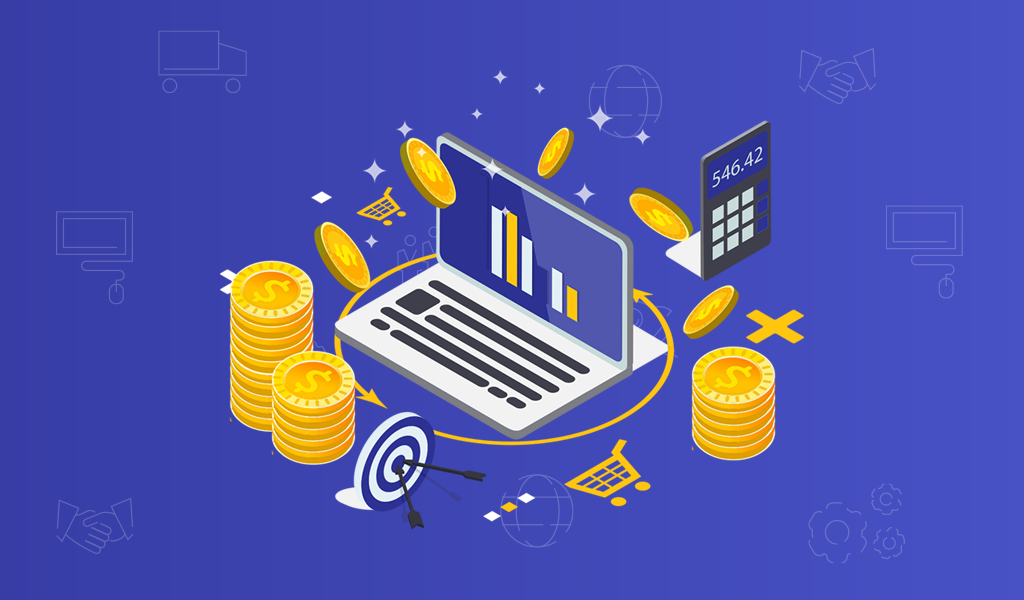
Retail season is always stressful; however, as the COVID-19 pandemic continues to rage, uncertainty and risk are steadily building up throughout both the supply and distribution chains.
In this post, we explore three operational risk factors which are cause for concern over the next six or seven weeks until the peak season has passed:
- Inbound logistics delays
- Warehousing and order fulfillment delays
- Outbound logistics delays
Inbound Logistics Delays
COVID-19 has been an event unlike any other in the history of the globalized economy. Its ramifications were first felt in February as China’s strict quarantine kept manufacturers from reopening for several weeks. In the days that followed, much of the rest of the world went into quarantine and supply chains buckled once again – this time as capacity dried up and PPE took full priority. Of course, the world has since largely reopened; however, inbound logistics – both foreign and domestic – remain sluggish. Furthermore, as COVID-19 case levels surge as we head into November, it certainly isn’t beyond the realm of possibility that large parts of the world will materially tighten up once more – inevitably degrading both manufacturing and logistics capacity and lengthening delays.
Warehousing and Order Fulfillment Delays
In the eCommerce order fulfillment space, the primary COVID-19-related concern (aside from safety, health, and wellness) is the maintenance of staffing levels adequate to handle not only expected volume, but periodic spikes as well. For eCommerce sellers handling order fulfillment in-house, the risk of an operational shutdown due to a COVID-19 outbreak amongst a small (and difficult to augment) staff may seem remote; however, if it happens in early- to mid-December, the brand-implications could be particularly severe if contingency plans cannot be immediately and successfully executed. At IronLinx Fulfillment, we have been working for months to incorporate a number of rigid practices and safeguards (including the physical separation of employees, redundant operating setups, and the development of a large pool of available substitutes, among other things) designed to minimize both the likelihood and/or impact of a COVID-19-related disruption.
Outbound Logistics Delays
Throughout the pandemic, domestic carrier delays have been noticeable, but especially so in the beginning of the summer. Heading into retail season, the primary carriers have all published guaranteed holiday delivery dates by service class; however, if conditions continue to deteriorate in the coming weeks, it wouldn’t be a surprise if many of these cutoffs end up shifting to earlier dates. Under normal circumstances, the carriers are able to materially staff up with temporary employees during peak season; however, COVID-19-related unemployment, fear, and safety protocols make this task much easier said than done this year.
A Few Suggestions
In our opinion, eCommerce sellers should plan for material delays in the coming weeks. Throughout most of the year, orders can be a day or two late without causing too much trouble; however, during the holidays, delays can do a substantial amount of long-term brand damage.
A few suggestions:
- If possible, front-load order volume into November and the earliest days of December – if things get messy, mid-December could easily descend into pure bedlam.
- Do not trust the guaranteed cutoff dates announced by the carriers – orders placed past December 13th are likely going to be pushing the envelope (unless expedited service classes are being utilized).
- Avoid overselling products which aren’t expected to arrive until December – any and all parts of the supply and distribution chains can easily buckle and make timely delivery either impossible or brutally expensive.
Recent Comments