News and Insights
E-commerce, Logistics, and Small Business Management
Baby Product Order Fulfillment: Special Packaging and Handling Needs
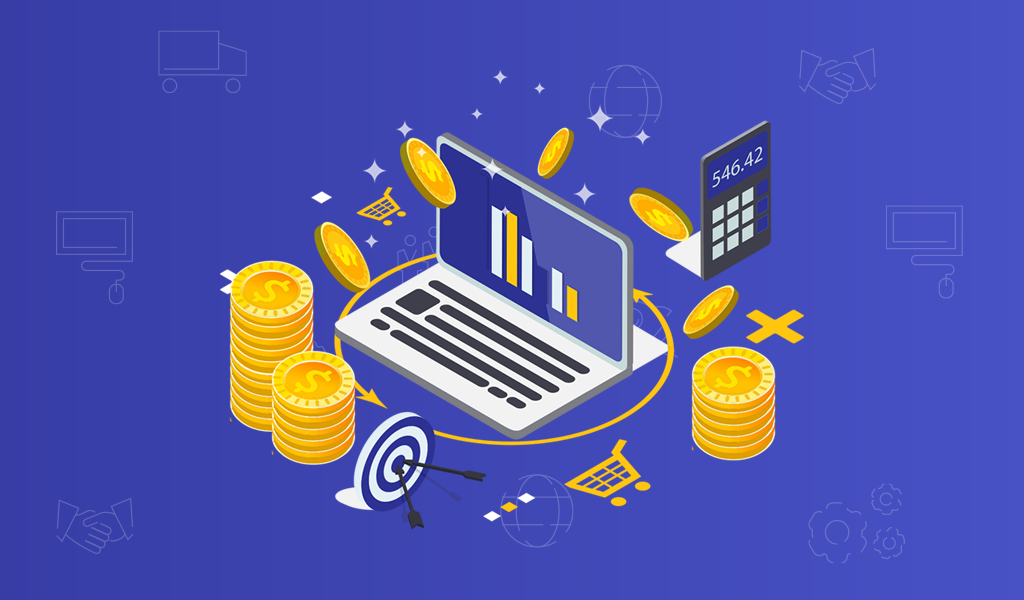
Due to the special packaging and handling requirements common to many of the product types in the category, baby product order fulfillment is not only uniquely challenging, but oftentimes much more expensive than anticipated by new entrants in the eCommerce space.
In this post, we explore the following:
- Fragility
- Temperature sensitivity
- Expiration dates
- Unboxing
Baby Product Order Fulfillment: Fragility
Many baby products are fragile. Consider, for instance, formula, food, or beverages which tend to be either encased or bottled in glass, hard plastic, or flexible pouches – all of which are susceptible to damage in transit. To minimize the likelihood of breakage, corrugated cartons (in place of bubblemailers or polymailers), rigid inserts, and some form of void fill (kraft paper, packing peanuts, shredded paper, etc.) are often required. Materials such as these significantly increase not only packaging fees, but handling fees (due to complexity and lost efficiency at the fulfillment level) and shipping fees (due to increased weight and/or dimensional weight) as well. Creams, lotions, sunscreens, and other ointments present their own unique challenges as their respective containers (generally bottles, tubes, or jars) tend to be susceptible to either crushing and/or otherwise breaking open in transit – ruining not only the affected item(s), but the overall presentation of companion products and marketing materials as well.
A few tips:
- When in doubt, use more protective materials as opposed to less.
- Keep in mind, however, that the use of corrugated cartons, rigid inserts, and void fill increases materials, handling, and shipping costs – the latter being especially problematic if the additional weight of the packaging materials takes things above one pound (which is a major demarcation line with most carriers).
- Consider using plastic bags and/or adhesive strips (to hold caps in place) for liquids.
Baby Product Order Fulfillment: Temperature Sensitivity
Many baby products do not handle either extreme temperatures and/or humidity well. Again, consider formula, food, or beverages – all of which can be rendered unsafe for consumption if exposed to heat, cold, or humidity for extended periods of time. For items such as these, climate-controlled storage is a must – at least, during the warmer months of the year (freezing temperatures and buildings generally don’t pair well, so the winter months tend to be less problematic as facilities are almost always heated). Beyond storage, keep in mind that baby products can also be damaged by heat, cold, and/or humidity either during or post-transit – it’s not uncommon for a parcel left unattended on a scorching hot porch, for instance, to be ruined before the intended recipient ever takes possession of it.
A few tips:
- Most temperature- and humidity-based problems occur in the summer; therefore, make sure that seasonal warehouse conditions are adequate for safe storage and consider faster shipping methods, if economically feasible, to reduce the likelihood of damage occurring in transit.
- Many fulfillment companies offer both climate-controlled and non-climate-controlled storage options – consider leveraging non-climate-controlled storage during milder times of the year to reduce costs (this does carry some risk, but it is quite common).
- If utilizing insulated or other specialized packaging materials, don’t lose sight of the potential upwards pressure that such materials put on both handling and shipping costs (more on this below).
Baby Product Order Fulfillment: Expiration Dates
Expiration dates make fulfillment a bit more complicated when different lots (batches) overlap in storage. When newer lots are received, it’s easy for them to end up in front of older lots which then proceed to age on the shelf – potentially leading to product expiration for those units which do not properly cycle through. There are formalized processes – generally known as “lot control” – which can prevent these types of problems; however, they require additional barcoding and handling which tends to increase the costs associated with both receiving and order fulfillment.
A few tips:
- Informal lot-control is sometimes possible (it necessitates the physical separation of different batches and the use of fulfillment staff with substantial account-specific knowledge); however, as a human-driven process, it is inherently error-prone (we only utilize informal lot-control processes at IronLinx as a temporary, one-off type of solution).
- Many expiration-oriented problems are driven by manufacturers shipping borderline “aged” products in the first place – receiving processes, therefore, should be developed to uncover these instances, if possible, before they become customer-facing.
Baby Product Order Fulfillment: Unboxing
Higher-end unboxing experiences are common in the baby product space. Given the emotional, gifting, and competitive aspects of many purchases in the category, this makes a lot of sense; however, perhaps more than any other factor, unboxing tends to significantly drive up costs. Custom packaging materials, for instance, are almost always more expensive than generic alternatives – plus, they are often treated as independent SKUs when it comes to storage and picking fee structures. Beyond the materials, special product arrangement or presentation also increases pick and pack time (and, by extension, fees). Frequently, though, the most substantial impact of unboxing comes in the form of increased shipping costs due to the weight (either actual or dimensional) added by the materials utilized.
A few tips:
- Unboxing is overrated – especially for firms which are materially resource-constrained.
- Complex packouts materially impact all aspects of a firm’s fulfillment profile – with the most severe cost implications oftentimes arising on the shipping side (especially if packaging and presentation drive actual weight above the one-pound demarcation line).
- The savings generated through the bulk purchase of customized packaging materials are often eroded by higher storage costs.
Conclusions
In fulfillment, anything is possible; however, as needs become more complex, keep in mind that costs often escalate quickly – and not just in the obvious way(s). In our nearly two decades of experience as an order fulfillment provider, our advice is generally to keep things as simple as possible.
Recent Comments