News and Insights
E-commerce, Logistics, and Small Business Management
Wholesale Pick Accuracy: Preventing Errors at Scale in Multi-SKU Jewelry Orders
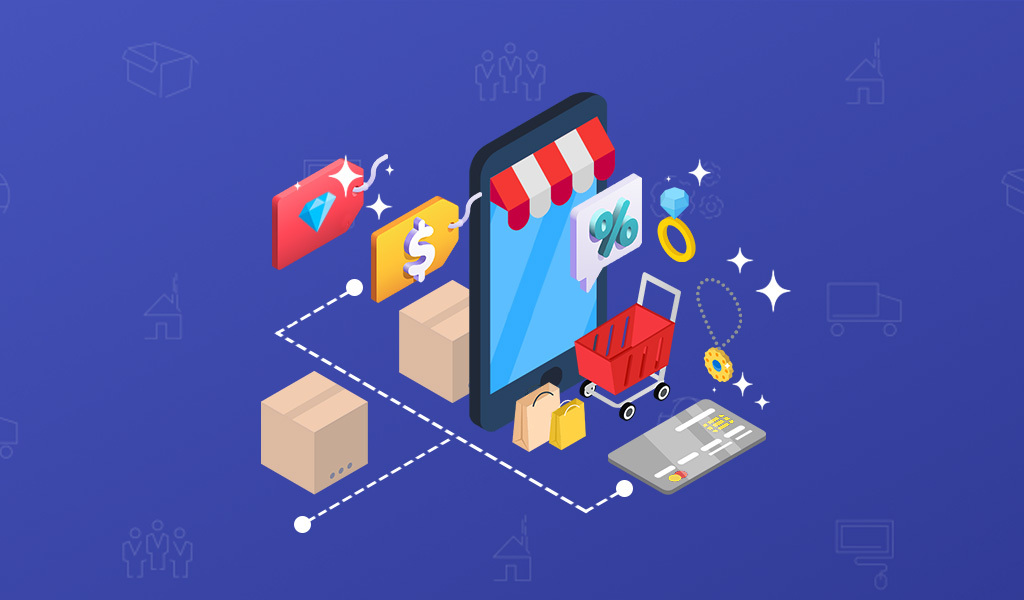
In direct-to-consumer jewelry fulfillment, picking mistakes are frustrating—but usually limited in scope. A missing item affects one customer, one box, and one relationship.
In wholesale jewelry fulfillment, a picking error can affect an entire floor set, multi-store rollout, or seasonal product launch. A miscount, substitution, or missing SKU doesn’t just cause inconvenience—it can cause revenue loss, penalties, and reputational damage that impacts your entire brand.
That’s why wholesale fulfillment requires a fundamentally different approach to pick accuracy—one that’s workflow-driven, system-supported, and built to scale.
Why Wholesale Picking Is So Prone to Error
Wholesale jewelry orders aren’t just larger versions of DTC shipments. They’re more complex, more varied, and often more time-sensitive.
What makes them risky?
- High SKU count per order – A single wholesale order may contain dozens of different SKUs, often with small but critical differences (e.g., chain length, plating color, earring back style).
- Deep line-item quantities – It’s not 1–2 units per SKU—it’s 20, 50, or 100+ units per line.
- Close product resemblance – Visual confirmation isn’t enough. Similar-looking items can have different UPCs or PO eligibility.
- Mixed configuration expectations – Some SKUs are packed as pre-packs, others as full-case quantities, and still others as loose stock.
- PO-level dependencies – Every item must match what the buyer approved, down to variant, packaging spec, and count.
The risk of error rises exponentially with volume—and without structured safeguards, mistakes are inevitable.
What Wholesale-Specific Pick Accuracy Requires
A fulfillment partner serving wholesale jewelry brands must have more than basic inventory control. They need structured processes and real-time verification at every step of the pick path.
Here’s what that should include:
1. Scan-Based Picking Workflows
Manual, paper-based picking may be acceptable for small, low-SKU DTC orders—but it’s not enough for wholesale.
Wholesale pick accuracy starts with:
- Barcode scanning at the item level – Every picked unit is validated against the order before it’s binned or packed.
- Bin-location logic – Pickers are routed efficiently to avoid misplacement or cross-contamination of SKUs.
- Live feedback for exceptions – If a picker scans the wrong item or over-picks a line, the system should catch it immediately.
This transforms picking from a best-guess task into a verified step in the fulfillment chain.
2. Multi-Line Order Validation
In wholesale, getting most of the order right isn’t good enough. Buyers expect perfect execution—especially when products are headed for retail displays or resale.
To meet that expectation, your fulfillment workflow should include:
- Line-by-line confirmation checkpoints – All SKUs and counts are reviewed before the packout begins.
- System flags for backordered or shorted lines – So issues can be communicated proactively—not discovered after delivery.
- Optional second-stage validation – A team lead or auditor can re-scan or spot-check high-priority accounts or high-risk orders.
Every step should reduce the opportunity for human error—not rely on someone “being careful.”
3. Channel-Linked Inventory Accuracy
Accurate picking depends on accurate inventory. If your WMS doesn’t track inventory in real time—and segment it by channel—you’re setting your team up to fail.
Wholesale picking workflows require:
- Live quantity tracking – Across all SKUs, variants, and storage locations.
- Channel-based allocation – So units reserved for wholesale aren’t pulled for DTC by mistake.
- Real-time error flags – For undercounts, over-picks, or missing bin assignments.
Picking accuracy is only as good as the data behind it.
4. Physical and Procedural Controls
Sometimes, the biggest difference between success and failure comes down to the environment and discipline of the operation.
That means:
- Clean physical layout – Well-marked pick zones, logical SKU organization, and uncluttered aisles.
- SKU separation protocols – Visually similar SKUs should be stored apart and labeled clearly.
- Clear SOPs for multi-picker orders – When multiple team members work on one order, there must be a controlled handoff process.
You can’t build precision on a messy floor.
Common Pitfalls to Avoid
Brands and fulfillment partners alike often underestimate the scale of risk in wholesale pick workflows. Here are some pitfalls to avoid:
- Visual picking – Relying on look alone leads to substitution errors, especially in jewelry.
- No second validation step – One mistake in a 40-line order can void the whole shipment.
- Pickers multitasking across channels – Switching between DTC and wholesale increases the chance of slippage.
- No audit trail – If no one knows who picked what, you can’t diagnose root causes when something goes wrong.
Wholesale fulfillment doesn’t just need structure—it needs accountability.
Final Thoughts: Accuracy Is Leverage in Wholesale
Wholesale buyers work with brands they can trust. If you consistently ship the right items, in the right quantities, with no surprises, you earn that trust—and the reorders that follow.
But if every PO becomes a gamble? You’ll lose shelf space and sales to brands that built a stronger fulfillment foundation.
Want help building pick accuracy into your wholesale operation? Let’s talk!
Recent Comments