News and Insights
E-commerce, Logistics, and Small Business Management
Preventing Damage, Tarnish, and Loss in Jewelry Fulfillment
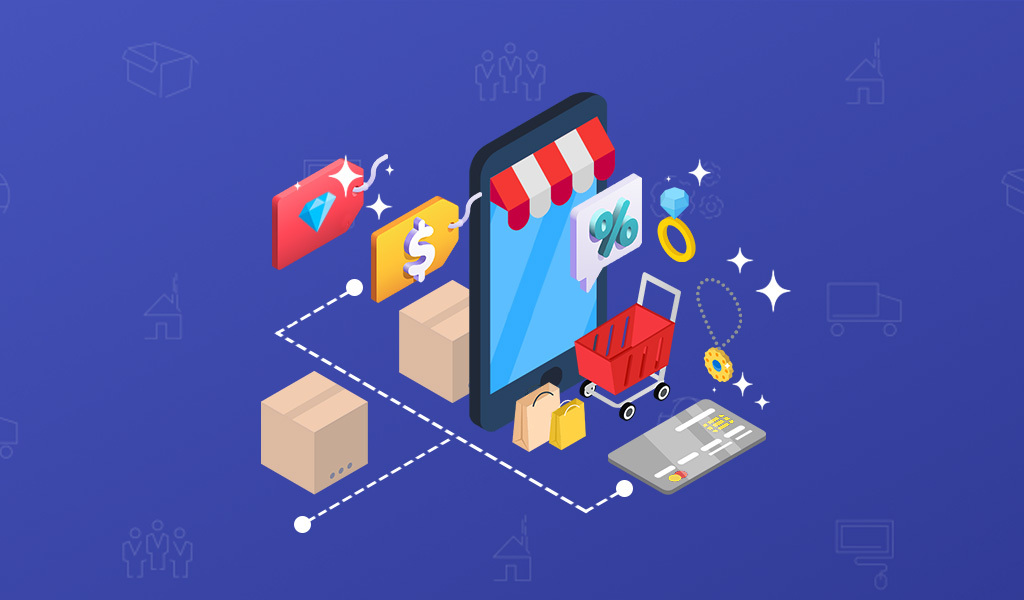
Fashion jewelry may be small and lightweight, but it brings oversized fulfillment challenges—especially for fast-growing brands. Unlike sturdier items, these delicate pieces are vulnerable at nearly every stage: from storage and internal transfers to final pack-out and shipping. A bent earring hook, a scuffed pendant, or a tarnished finish can turn into a return—or worse, a lost customer.
This guide outlines the three most common fulfillment risks in fashion jewelry—damage, tarnish, and loss—and how to prevent them before they undermine your operations. Through better systems, protective materials, and a culture of careful handling, you can scale your business without compromising quality.
1. Preventing Damage: Soft Systems for Fragile Goods
Jewelry often gets damaged long before it reaches the customer. Rough bins, fast hands, and careless movement between stations can lead to scratches, dents, or bent pieces—especially with thin, plated, or delicately assembled items.
Key Strategies:
- Package early, not just at the end.
Pre-bag or pre-box inventory whenever possible to minimize raw item exposure across fulfillment stages. - Avoid unnecessary touchpoints.
Limit how many times an item is handled before it ships. Review your workflows to eliminate redundant steps. - Keep storage simple—but separate.
Store items in a way that prevents friction. Separate pieces by type or weight, and avoid dumping different styles into the same bin. - Use soft dividers or sleeves where needed.
For more delicate pieces, consider low-cost protective options like poly bags, foam inserts, or even folded tissue between items. - Train for care, not just speed.
Remind your team that jewelry isn’t apparel or bulk goods. Reinforce the importance of careful transfers, clean hands, and visual inspections.
2. Preventing Tarnish: Control the Environment, Not Just the Packaging
Tarnish is one of the most frustrating—and often preventable—fulfillment issues. It’s subtle, slow, and hard to reverse. Brands working with plated, mixed-metal, or untreated brass designs are especially vulnerable.
Key Strategies:
- Separate metals by material or finish.
Avoid co-storing brass, silver, and plated items together in bulk bins. Cross-contact accelerates chemical reactions. - Add anti-tarnish strips to long-term storage.
These low-cost inserts can significantly reduce oxidation, especially in high-humidity areas or during slower seasons. - Avoid exposure to sunlight or HVAC vents.
Keep jewelry storage away from direct light or airflow that fluctuates temperature or humidity across the day. - Don’t rely solely on retail packaging for protection.
If items arrive pre-bagged, confirm that materials are tarnish-safe and that closures are sealed. Rebag if necessary. - Train your team to flag early signs.
A faint darkening or discoloration is often the first sign of tarnish. Encourage staff to set questionable pieces aside before they reach the customer.
3. Preventing Loss: Structure Inventory to Guard the Smallest Components
Jewelry loss isn’t always theft—it’s disorganization. Small items go missing when bins are unlabeled, categories are mixed, or internal processes are undocumented.
Key Strategies:
- Never store unpackaged inventory in open bins.
Small components should be bagged and labeled—even if they’re not sellable yet. - Use clearly segregated storage zones.
Create visual and logical systems to separate in-stock, in-process, QC-hold, and return inventory. Avoid commingling items in a rush. - Document touchpoints between teams.
Any time inventory leaves a storage location—for photography, quality checks, or kitting—it should be signed out and signed back in. - Avoid overstocking bins or drawers.
Small pieces disappear easily—under foam, in corners, or beneath other items. Keep bins light and organized so you can see everything at a glance. - Make inventory visibility part of team culture.
Everyone who handles product—whether for QC, kitting, or returns—should know how easy it is to lose small items. Reinforce habits like labeling, logging, and double-checking bins before moving on.
Final Thoughts
Damage, tarnish, and loss aren’t flukes—they’re signals. They reveal where systems are rushed, storage is neglected, or processes aren’t built to match the product’s sensitivity.
Preventing these issues starts upstream. Protecting jewelry isn’t just about bubble wrap and mailers—it’s about thoughtful handling, smart storage, and a culture that treats every piece like it matters.
Your customer doesn’t see your fulfillment operation—just the result. To them, these details are your brand.
Interested in outsourcing fulfillment? Let’s talk!
Recent Comments