News and Insights
E-commerce, Logistics, and Small Business Management
How to Organize Your Jewelry Inventory for Faster, Error-Free Fulfillment
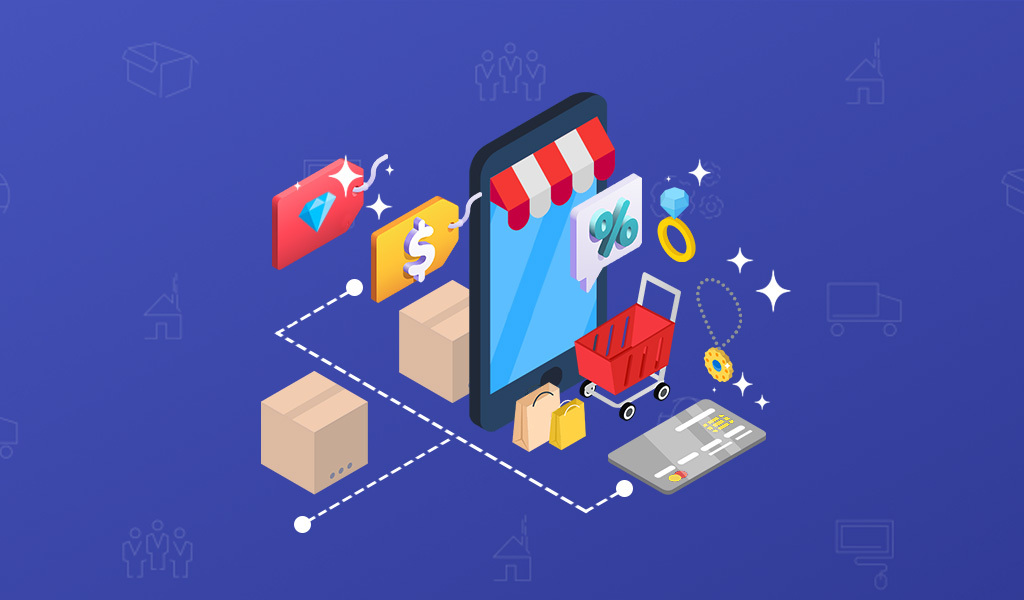
If you’ve ever scrambled to find a specific earring or triple-checked a necklace before sealing the box, you’re not alone. Packing jewelry orders can be tricky—especially with tiny pieces, similar styles, and custom combinations. It’s easy to focus on the comforting rhythm of fulfillment: folding tissue, nestling pieces into presentation packaging, and handwriting notes. But when every order feels a little more chaotic than the last, the issue often isn’t how you’re packing—it’s how your inventory is organized behind the scenes.
A well-organized inventory system lays the groundwork for faster packing, fewer mistakes, and a smoother day-to-day rhythm. When every item has a clear, consistent home, you’re not second-guessing yourself or losing time hunting for pieces—you’re simply following a flow that works. Whether you’re fulfilling orders solo or starting to bring in help, good organization makes the entire process feel lighter and more manageable.
In this post, which is part of our ongoing series on jewelry order fulfillment, we walk through a few simple strategies that can help you get organized—and stay that way—as your business grows.
1. Barcodes Are Your Friend
Manual inventory identification might work when you’re only shipping a few orders a week—but as volume and catalog size increase, it quickly becomes a source of frustration and error. Digging through bins, squinting at tiny SKU tags, or relying on memory to tell similar items apart slows everything down and makes mistakes almost inevitable. One mix-up might not seem like a big deal, but over time, mispicks, delays, and returns can quietly chip away at both your profit margins and your customers’ trust. The more orders you handle, the more those little inefficiencies start to pile up—and manual processes simply can’t keep pace.
Best practices:
- Barcode each SKU, even if you’re not using a barcode scanner yet. This will make future upgrades easier.
- Choose a barcode format and label size you can stick with long-term—consistency now will save you time when you scale or switch to a scanning system later.
- As your order volume increases, consider investing in barcode scanning technology to speed up picking and ensure accuracy. Scanning barcodes during order fulfillment is faster and far less error-prone than searching for product names manually.
2. Assign Every SKU a Home
A cluttered storage system might seem manageable at first—but as your inventory grows, it becomes a recipe for confusion. Similar-looking pieces get mixed up, bestsellers get buried, and finding the right item starts to feel more like a scavenger hunt than a workflow. Even if you know your products by heart, it’s easy to grab the wrong variant or miss a detail under pressure. Over time, the delays, mispicks, and re-dos don’t just slow you down—they create stress, increase returns, and chip away at the trust you’ve built with your customers.
Best practices:
- Assign every SKU its own dedicated location in your storage space. Use bins, trays, or labeled shelves for each product category.
- Clearly label each location with the SKU name or number, and ensure the labeling is easy to read.
- When possible, organize products by type, size, or material—this keeps things simple and reduces the chance of mix-ups.
- Bestsellers and frequently picked items should be within easy reach for optimized picking and packing.
3. Track What’s Moving—And What’s Not
A well-organized space is only half the equation. To truly streamline your fulfillment process, you need to understand what’s moving quickly—and what’s just taking up space. Without a clear view of your sales trends, you risk overstocking slow sellers or constantly running low on popular items, both of which can disrupt fulfillment and lead to rushed decisions.
Best practices:
- Review your sales data regularly to identify your fastest- and slowest-moving SKUs.
- Adjust your storage layout as needed—move bestsellers to more accessible locations and rotate out items that aren’t pulling their weight.
- Use this insight to guide future purchasing and kitting decisions, so you’re not packing inventory that isn’t moving.
- Consider creating a small overflow or clearance area to manage excess stock without cluttering your main fulfillment zone.
4. Create a Simple System for Inbound Inventory
Even the tidiest storage system falls apart if your inventory doesn’t actually make it onto the shelves. New arrivals, restocks, and even returned items can easily pile up if you don’t have a clear process for receiving and/or reintegrating them. Unlabeled products get misplaced, items meant for bundles end up packed solo, and returns sit in limbo. Without structure on the front end, even the best-organized shelves can fall into disarray. Building a simple, repeatable system for getting inventory into your system is just as important as how you store it.
Best practices:
- Create a designated “new arrivals” zone for incoming inventory, so nothing gets mixed in with active stock before it’s been processed.
- Label every item and assign a storage location before it leaves the receiving area—this keeps your system clean and traceable from the start.
- If a shipment arrives missing components or awaiting inspection, place it in a clearly marked holding area so it doesn’t get mixed with active stock.
- Use a simple receiving checklist or log to note what’s arrived, what’s been shelved, and what still needs action—this is especially helpful when dealing with partial shipments or returned stock.
5. Keep Packaging and Presentation Materials Ready to Go
When you’re trying to ship quickly and consistently, digging for tissue paper, thank-you cards, or jewelry pouches slows everything down. Presentation is a big part of the customer experience—but if your materials are scattered, damaged, or stored inefficiently, it creates friction in your workflow. A dedicated, organized setup for packaging supplies makes it easier to maintain quality and move through orders without missing a beat.
Best practices:
- Store your most-used packaging items—like tissue, stickers, jewelry pouches, and insert cards—in one centralized, easy-to-access area.
- Pre-bundle or pre-kit packaging components during slower times (e.g., tissue + pouch + thank-you card) to speed up your process during busy periods.
- Always keep backup stock of critical items nearby, so you’re not scrambling mid-pack when supplies run low.
Conclusion
The way you organize your inventory sets the tone for everything that comes after. Before a single order gets packed, the right systems quietly keep things running—preventing damage, reducing mistakes, easing stress, and helping you move with confidence. A little structure upfront goes a long way, especially as your business grows and the pace picks up.
Need help thinking through your next step in jewelry fulfillment? Let’s talk.
Recent Comments